What Is EMC and Why Does It Matter?
Electromagnetic Compatibility (EMC) is the ability of electronic devices to coexist without stepping on each other’s toes—or rather, their electromagnetic fields. It’s a dual challenge: your device must not emit excessive electromagnetic interference (EMI) that disrupts neighbors, and it must withstand external EMI without faltering. Think of it as the difference between a quiet library and a rock concert—EMC ensures your electronics stay calm and collected, no matter the noise around them. In a world packed with gadgets, from smartphones to industrial robots, poor EMC can lead to glitches, data loss, or downright dangerous failures. At CustomPowerLabs, we tackle this head-on with custom solutions like **shielded components** to dampen EMI at its source and **metal shrouds** to completely encase PCBs, keeping noise in and out under control. Our goal? Bulletproof reliability and compliance with the toughest standards.
Methods to Achieve EMC: Locking Down EMI
EMC isn’t magic—it’s engineering precision. Here’s how we make it happen, with a heavy emphasis on shielding:
Shielding: The EMI Force Field
Shielding is your first and fiercest weapon against EMI. By wrapping components or entire boards in conductive materials, we block electromagnetic fields from sneaking in or out. **Shielded components**—like inductors, transformers, or connectors—come with built-in conductive layers (often copper or steel) that trap their own EMI, stopping it from radiating into nearby circuits. Picture a noisy generator in a soundproof box; it still runs, but the racket stays inside. For the ultimate protection, we go bigger: a **metal shroud**—think aluminum or stainless steel—can encase your entire PCB, forming a Faraday cage. This isn’t just a shield; it’s a fortress. Noise from outside (like radio signals or power line spikes) gets bounced away, and internal EMI (from switching regulators or clocks) stays locked up tight. At CustomPowerLabs, we design these shields to your exact specs, balancing weight, cost, and performance for jaw-dropping EMI reduction.
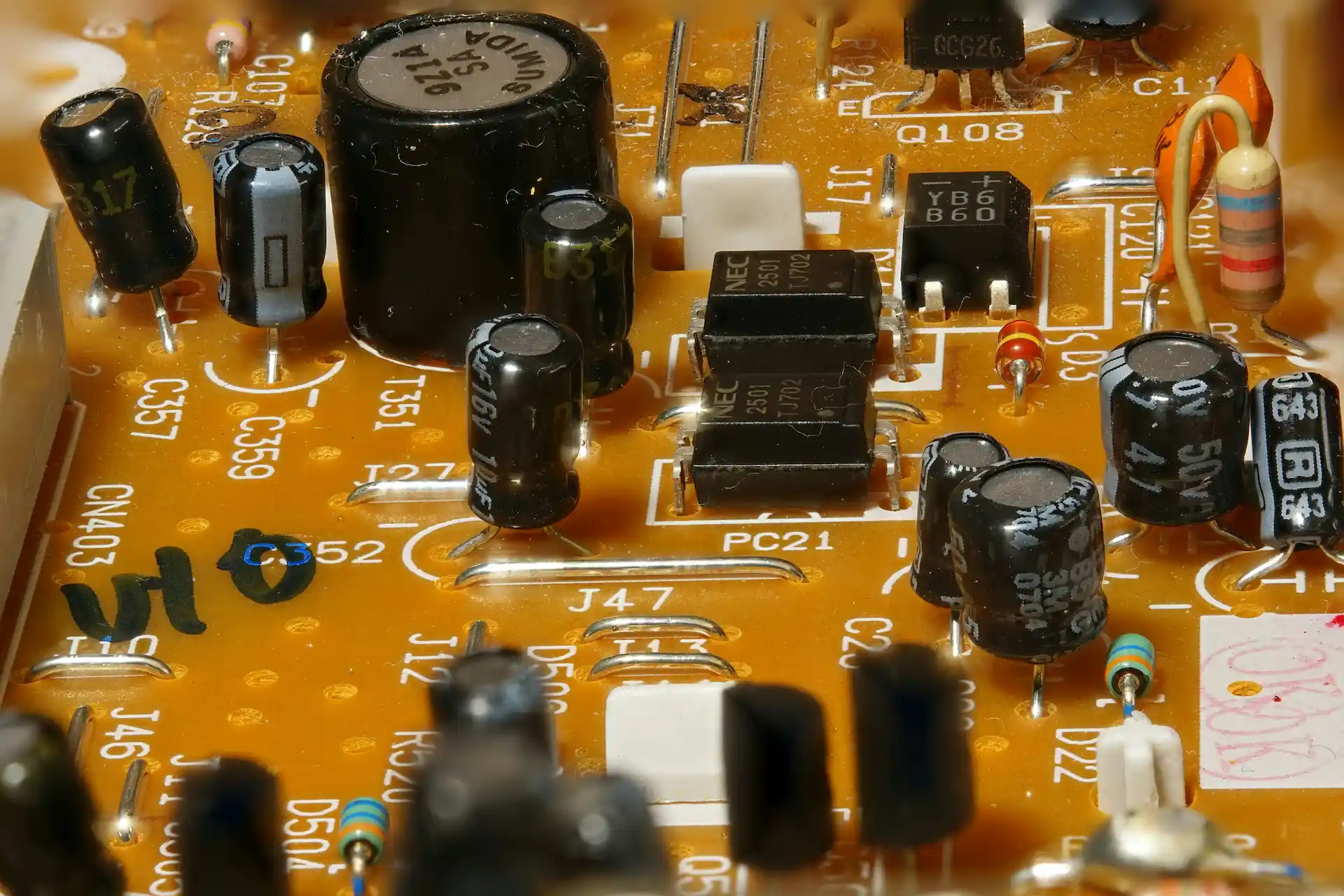
Filtering: Sifting Out the Noise
Even with shielding, some EMI sneaks through power or signal lines. That’s where filters come in—they’re like bouncers at a club, letting the good signals in and kicking noise to the curb. Low-pass filters zap high-frequency EMI while preserving your data or power flow. Ferrite beads target specific frequencies, acting as EMI sponges without adding bulk. We also use capacitors and chokes in custom configurations to tackle stubborn noise profiles. Whether it’s a 50 Hz hum or a 2.4 GHz Wi-Fi spike, CustomPowerLabs crafts filter networks that keep your circuits pristine.
Grounding: Steering EMI Away
Grounding is the unsung hero of EMC. It gives EMI currents a fast track out of your system, away from sensitive areas. We design **ground planes**—large, low-impedance copper layers—to soak up stray currents and shunt them to earth. **Star grounding** keeps noisy and quiet circuits separate, avoiding crosstalk. And for mixed-signal boards, we split grounds to isolate analog from digital chaos. Add in tricks like via stitching and guard traces, and your PCB becomes an EMI-proof fortress—all courtesy of CustomPowerLabs’ obsessive attention to detail.
Layout Optimization: EMI’s Worst Enemy
A sloppy PCB layout is an EMI playground. Long traces turn into antennas, broadcasting noise far and wide. Poor component placement couples EMI into quiet zones. We fight back with tight designs: short traces, separated power and signal paths, and differential signaling for critical lines. We also bury sensitive traces between ground planes and use shielding vias to box in EMI hotspots. It’s painstaking work, but it slashes EMI and boosts immunity—making your design a compliance champ.
Where EMC Screening Saves the Day
EMC isn’t optional in these high-stakes fields—our shielded solutions shine here:
- Medical Devices: EMI in a hospital can throw off ECGs or crash ventilators. Our metal shrouds and shielded components keep life-saving gear humming.
- Automotive: Cars are EMI jungles—radios, sensors, and motors all fighting for airtime. We shield ECUs and infotainment to keep them in sync.
- Industrial: Factory floors buzz with EMI from motors and welders. Our designs ensure PLCs and sensors stay rock-steady.
- Aerospace & Defense: Radar, comms, and lightning strikes test EMC limits. Our shrouds and shielding deliver mission-critical reliability.
- Consumer Electronics: Your smartwatch shouldn’t fry your earbuds. We keep everyday tech interference-free.
Benefits of Custom EMC Solutions
Why go custom with CustomPowerLabs? Because generic fixes don’t cut it:
- Perfect Fit: Shielded components and shrouds tailored to your noise profile—no guesswork, no gaps.
- Compact Design: Integrated shielding shrinks footprints, ditching bulky retrofits.
- Compliance Made Easy: Meet FCC, CE, or MIL-STD-461 without breaking a sweat.
- Cost Efficiency: Smart shielding cuts part counts and rework, saving big on production runs.
- Peace of Mind: Our expertise and testing mean your product performs—period.
EMC Testing: We’ve Got You Covered
Design is half the battle—testing seals the deal. At CustomPowerLabs, we don’t just build EMC solutions; we prove they work. Our **in-house EMC lab** is packed with gear: anechoic chambers to kill reflections, spectrum analyzers to hunt emissions, and signal generators to simulate EMI hellscapes. We run **pre-compliance testing** early, catching issues before they tank your budget or timeline—think radiated emissions scans or conducted immunity checks. Found a hotspot? We tweak the shield, adjust the filter, or reroute a trace on the spot. For **full compliance**, we guide you through certified labs, prepping your design for standards like FCC Part 15, CISPR 22, or ISO 11452. We test emissions (what your device puts out) and immunity (what it can take), ensuring it’s a tank against EMI. Need a report for regulators? Done. From prototype to production, our testing slashes risks and speeds you to market.

FAQs About EMC Screening
How do shielded components reduce EMI?
Shielded components use conductive enclosures or coatings to prevent electromagnetic interference (EMI) from affecting nearby circuits. They act as a barrier, containing EMI within a specific region and preventing it from radiating outward.
How It Works:
- Conductive Shielding: Uses copper, aluminium, or metalized coatings to absorb and redirect EMI.
- Grounding Strategies: Proper grounding ensures interference is dissipated safely instead of causing cross-talk.
- Strategic Placement: Shielding is applied to high-frequency components, switching regulators, and RF-sensitive circuits.
Common Uses: RF transmitters, high-speed digital circuits, automotive electronics, and industrial controllers.
What’s the big deal with a metal shroud?
A metal shroud is a full PCB enclosure designed to block all EMI from entering or leaving a system. This provides complete protection for sensitive electronics operating in harsh or noisy environments.
Advantages of Metal Shrouds:
- Full EMI Containment: Prevents both incoming and outgoing interference, making it ideal for mission-critical systems.
- Durability & Environmental Protection: Shields against physical damage, dust, and moisture, ensuring long-term reliability.
- Essential for Compliance: Helps meet stringent EMI/EMC regulatory standards, reducing the risk of design failures.
Best for: Aerospace, medical devices, precision measurement instruments, and defence electronics.
Can’t I just use off-the-shelf parts for EMC?
While generic shielding components exist, they are often too bulky, too weak, or simply not optimized for your specific design. Custom shielding solutions ensure a perfect fit, better performance, and lower costs.
Why Custom EMC Solutions?
- Size Optimization: Off-the-shelf solutions may be too large, wasting PCB space and increasing weight.
- Cost Efficiency: Custom designs remove unnecessary materials and only include what’s needed.
- Performance Matching: Tailored solutions ensure the shielding meets exact frequency, material, and form factor requirements.
If you want maximum efficiency without overpaying for unnecessary shielding, a custom approach is always better.
What’s involved in EMC testing?
EMC testing evaluates whether a device meets electromagnetic compatibility standards by measuring both emissions (interference created by the device) and immunity (how well the device resists external EMI).
Key EMC Tests:
- Radiated Emissions: Measures the unintentional radiation of electromagnetic waves from a device.
- Conducted Emissions: Checks for EMI travelling through power or data cables.
- ESD (Electrostatic Discharge) Testing: Simulates electrostatic shocks (e.g., from human touch) to ensure device robustness.
- Surge & Transient Immunity: Tests how the device handles voltage spikes and power fluctuations.
- RF Immunity Testing: Ensures resistance against external radio frequency interference.
Passing EMC testing is critical for regulatory approval and prevents unexpected performance issues in the field.
Why choose CustomPowerLabs for EMC?
At CustomPowerLabs, we provide end-to-end EMC solutions, from shielding design to compliance testing. Our expertise ensures that your products meet all necessary standards while maintaining peak performance.
What We Offer:
- Custom Shielding Solutions: Tailored enclosures, PCB-level shielding, and ferrite bead integration.
- Pre-Compliance Testing: Catch EMC issues early before full certification testing.
- Expert Design Support: Optimized PCB layouts for noise reduction and electromagnetic shielding.
- Certified Testing Services: Ensures compliance with CE, FCC, CISPR, and MIL-STD EMC standards.
With CustomPowerLabs, you get a seamless EMC strategy—designed, tested, and certified in one place.
How does PCB design influence EMC performance?
Proper PCB layout is one of the most critical factors in minimizing EMI. A poorly designed board can radiate unwanted noise, interfere with nearby circuits, or fail EMC testing.
PCB Design Best Practices for EMC:
- Ground Planes: Use solid, uninterrupted ground planes to reduce EMI and improve signal integrity.
- Trace Routing: Minimize loop areas and keep high-speed traces short and well-shielded.
- Decoupling Capacitors: Place low-ESR capacitors near power pins to filter high-frequency noise.
- Layer Stack-Up Optimization: Multilayer PCBs with dedicated power and ground planes improve shielding.
By applying these principles, you can greatly improve EMC performance without excessive external shielding.
Ready to banish EMI for good? Contact us—let’s shield your project from the chaos!